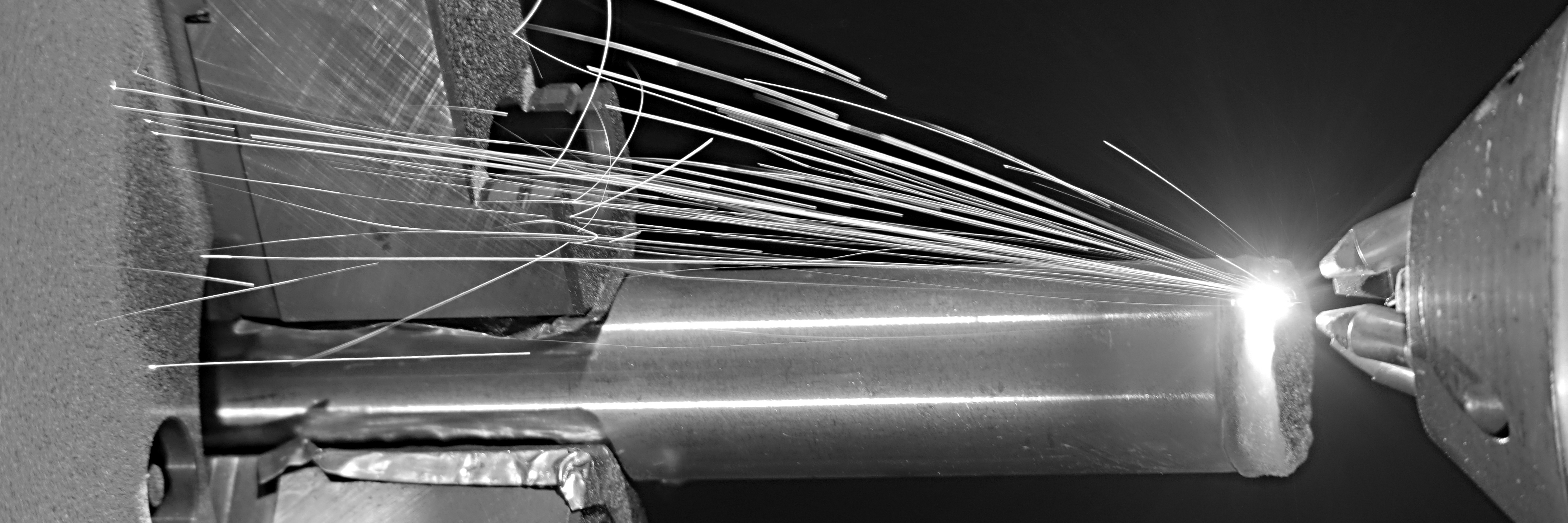
There’s a Better Solution for Equipment Breakdowns
Additive manufacturing offers a new, state-of-the art approach that restores equipment with unprecedented speed
properties.trackTitle
properties.trackSubtitle
Minimize Downtime, Maximize Productivity
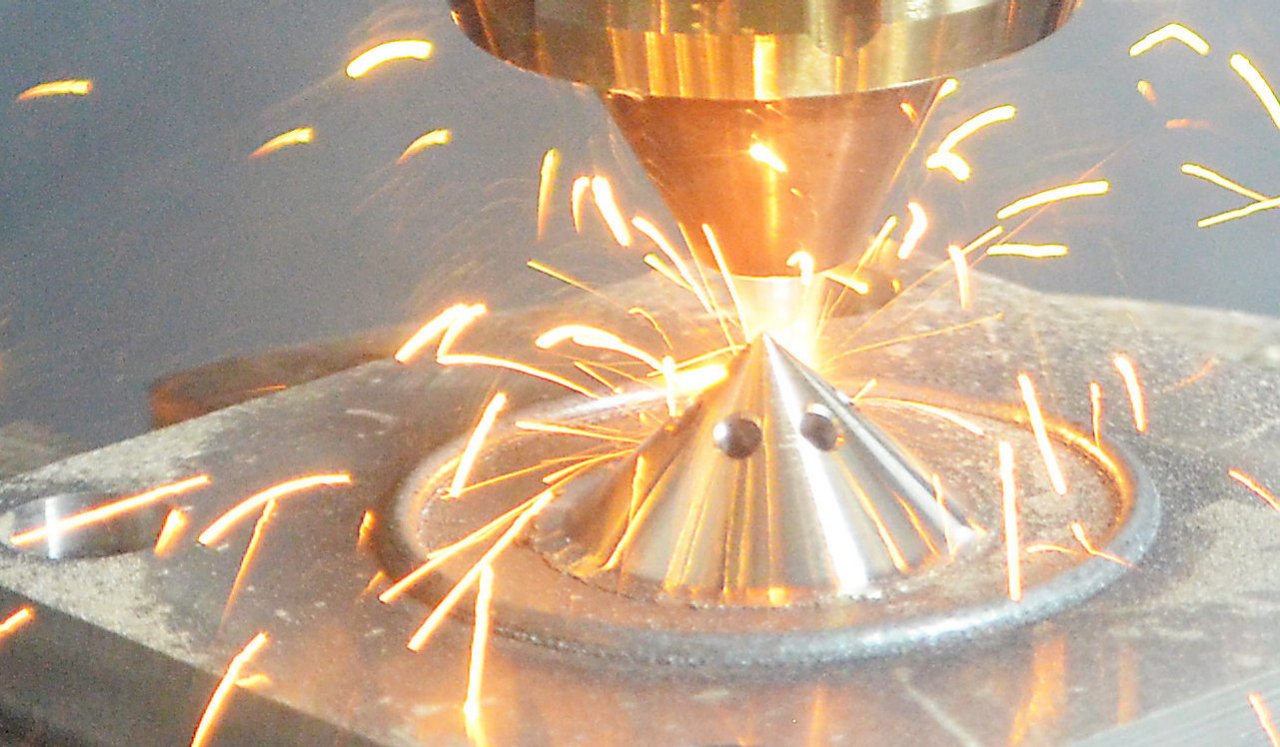
Equipment breakdown is a fact of life. And every moment of downtime is costly; a timely fix is crucial. But replacing broken or damaged parts can take months—especially for large or legacy machines that drive countless operations. HSB’s Additive Manufacturing for Equipment Breakdown (AM for EB) capability offers a remedy. Additive manufacturing marries the strength of traditional welding and fabrication with the power of 21st-century technology, delivering superlative parts in record time.
Don’t let a slow supply chain or lengthy build process stop business in its tracks; from small gears to worn bearing surfaces to large drive shafts, advanced AM can replace or repair parts quickly, across a stunning array of materials. Combined with HSB’s hands-on engineering know-how, this new approach to equipment breakdowns means getting back to work faster—and better.
The Strength of the Past Meets the Technology of the Future
Additive manufacturing is now a front-line application; it's transforming metals manufacturing across industries, from aerospace to oil and gas. The process, essentially an end-to-end fabrication technology, can not only build metal parts from scratch, but also repair or enhance existing parts—restoring them to former function, or even making them stronger and longer-lasting.
Flexible, by design: With the aid of Computer-Assisted Design programs, parts produced through additive manufacturing are built to spec, exactly. And, the software delivers added flexibility that can’t be easily achieved in traditional casting or welding. If experience has revealed that, for peak performance and minimal wear, a part needs to be altered by just a few cubic millimeters, the AM process can deliver a part that is custom designed to meet the individual needs of any given piece of equipment.
One and done: Parts are not only fabricated or repaired, but also put through any needed machining or milling processes. The result is a component that is ready to go from the moment the AM build chamber is opened and the finished part is removed.
Tested, and proved: Exhaustive tracking and testing is done. Sensors built into AM build chambers track material properties; afterward, facilities use imaging technology from CT scans to X-rays to ensure that finished pieces are sound. And, hardness and tensile strength are tested. Overall, fatigue tests of AM-produced parts have shown, again and again, that they are just as strong, if not more so, than components produced by traditional means.
Material possibilities: Additive manufacturing is used across a huge array of metals, from steel to aluminum to titanium, along with materials like diamond and graphite; it can also create innumerable alloys. Or, in the case of a repair, the AM process can deposit a different, more suitable metal on a legacy part, ensuring its longevity, and creating a stronger component than when the part was brand new. Because of the flexible build process, and the host of usable materials, AM is suited for replacement or repairs both large and small, both straightforward and complex.
Every minute of an equipment breakdown can cost money. And, if it goes on long enough, a breakdown can spell disaster for a business. Legacy parts must be located in a distant warehouse or shipped across oceans. Lead time for castings for a new part can be a year or more. Traditional replacement or repair can drag on…and on. HSB’s additive manufacturing approach can deliver a new or repaired part to the shop floor in a matter of days or weeks. It’s a new, cost-effective solution that is powerful, dependable, and flexible—and gets you back to work.
HSB Delivers a Hands-On, Diagnostic Approach
AM for EB: Backed by a Tradition of Engineering Excellence
For more than 150 years, industry has trusted HSB’s engineers to keep equipment safe, reliable, and productive. We’ve lasted this long precisely because of our approach to innovation. Our deep technical knowledge means we evaluate new technology according to exacting standards—and with an eye toward the next century. Our Additive Manufacturing for Equipment Breakdown offering is the next chapter in this tradition of innovation; it’s a new way to ensure our customers thrive.