What is the True Cost of Steam?
You're probably paying a lot more than you think
properties.trackTitle
properties.trackSubtitle
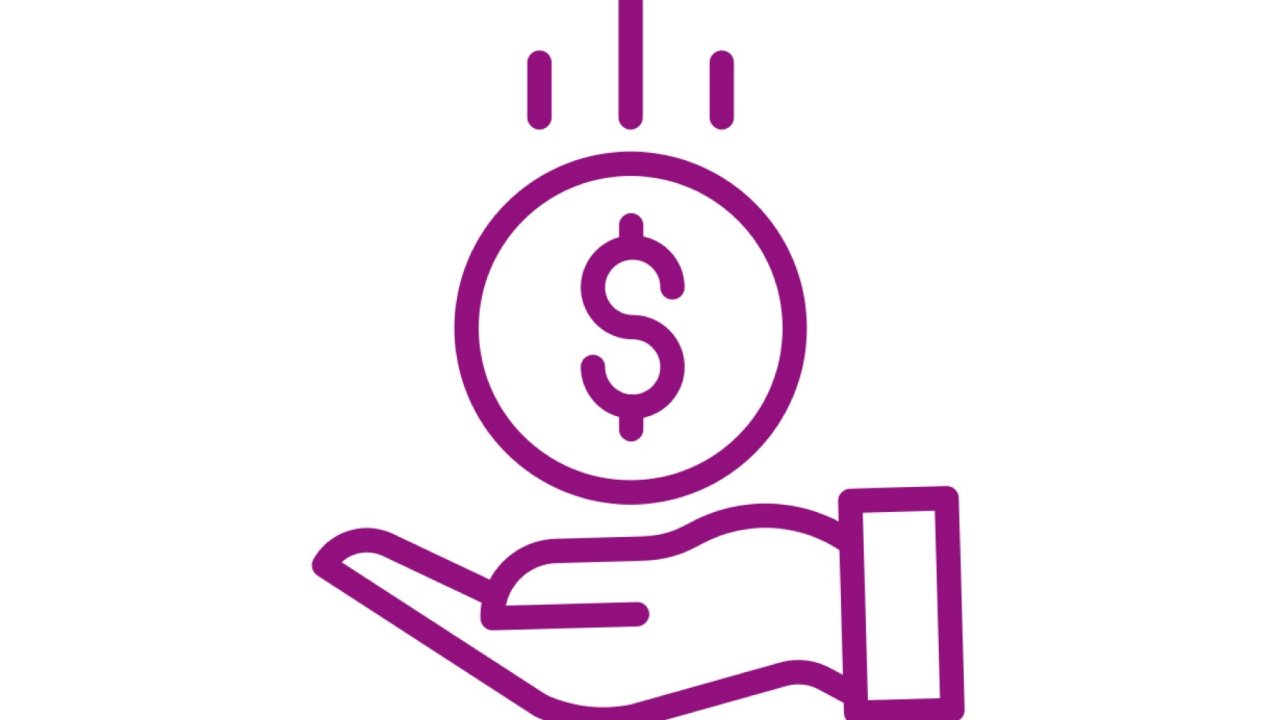
No two businesses are exactly alike; each requires unique expertise. But no matter your line of work, there is one basic requirement: a clear understanding of overhead costs. But for the countless industries that rely on steam — whether it’s process steam, clean steam, or steam for heat — this essential bit of accounting presents an enormous challenge. In other words, there’s a good chance that your steam is costing you far more than you realize.
Calculating the cost of steam might seem like a pretty straightforward operation. First, there’s the initial investment. A steam plant purchase requires hefty capital outlay. But that’s actually the least expensive part of the steam-generation process. Running the plant is far more costly.
There are the obvious costs (fuel, water), but there is a vast network of ancillary expenses that often stay out of sight — and that’s bad news for earnings.
Understanding the true cost of steam generation is crucial for a business to thrive.
Fully Loaded Costs
Maintaining your boilers is an enormous expense. There’s the cost of parts replacement, service calls, inspections, emissions costs, and calibrations to think about.
Operating the steam plant requires an expert workforce, which means paying for hiring and training; wages and overtime; benefits; and uniforms, tools, and other on-the-job employee needs.
Supplying boilers with consumables — everything from water treatment to filters to salt — is critical for proper steam production, but puts a big dent in annual budgets.
Finally, administration is costly. It takes time and expertise to oversee the maintenance and operations of the plant itself, and to make sure things are running smoothly and safely. Procurement, HR, inventory management, legal oversight, environmental consulting, insurance — all of these things divert valuable time and resources away from the most important thing of all: your core business.
Low Efficiency, Higher Costs
Even if every last operational cost is noted in scrupulous detail, the true cost of a steam system can still go unaccounted for — all because of an oft-misunderstood yet vitally important aspect of steam generation: system efficiency. Chances are, your system isn’t nearly as efficient as you think. And if your steam plant is leaky, that means you’re leaking money.
Boiler efficiency is key. Many boilers’ efficiency tops out around 82%. But a huge percentage of boilers clock in far, far lower — as low as 65% in some legacy systems. And each percentage point below the 82% efficiency benchmark can translate to hundreds of thousands of dollars in fuel costs per year.
But boiler efficiency is only one aspect of total system efficiency; there are dozens of other potential weak spots. And each point of efficiency lost translates to dollars lost.
Peak system performance, and the associated cost savings, is entirely feasible. But it requires expert management and oversight, and modern equipment — all of which are within reach, for no upfront costs, and a single, monthly payment. Steam-as-a-Service (SaaS) is a new approach to steam generation that puts your steam in the hands of experts, and allows you to focus on what is most important: your core business.